Problems in Sand Casting of Large Castings
Sand casting process is a common production process in large steel casting factories, and it is also a traditional casting method. Based on its own characteristics, it can process some small batches of castings. The process flow basically includes the following steps: sand molding, core making, pouring, sand dropping, polishing processing, and inspection. Today, we will summarize the issues related to sand casting through the processing of large-scale steel castings. We believe that these can bring you some help:
1. In the sand mixing stage, the production of molding sand and core sand is mainly used for molding, and a sand mixer is usually used to mix the new and old materials.
2. In the mold making stage, the mold can be processed according to the drawings. Wood mold, plastic mold and metal mold can be selected as templates, and the Makespan can be shortened.
3. The stage of molding, also known as core making, is an important part of the entire process. Once slight differences occur, subsequent processing will also affect product quality.
4. During the melting stage, suitable alloy materials can be selected based on the assigned chemical composition to form qualified molten metal. Large steel casting manufacturers usually use electric furnaces for their melting equipment.
5. Liquid pouring, using a molten iron ladle to pour the melted liquid into the prepared core, and the pouring speed needs to be controlled to allow the liquid to fill the entire cavity.
6. After pouring and waiting for the liquid to solidify, clean the sand at the gate and use a sandblasting machine for sandblasting, so that the surface of the casting is very clean.
7. For castings with special requirements, clean and polish them, perform simple machining, and remove burrs to make the castings look very smooth and clean.
8. During the process of cleaning or processing, a batch of unqualified products have already been removed during product inspection. However, large steel foundries still need to inspect them before the final process leaves the factory.
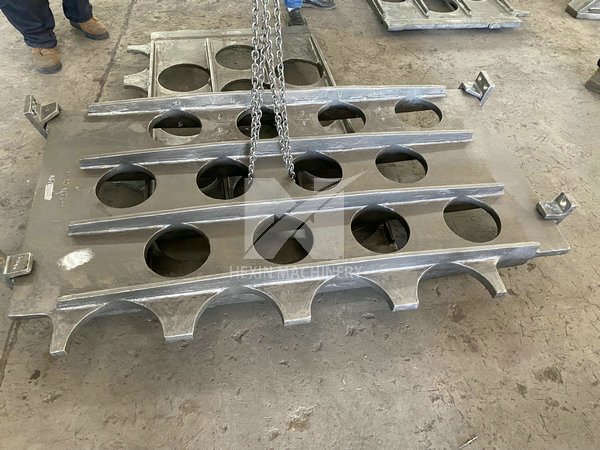