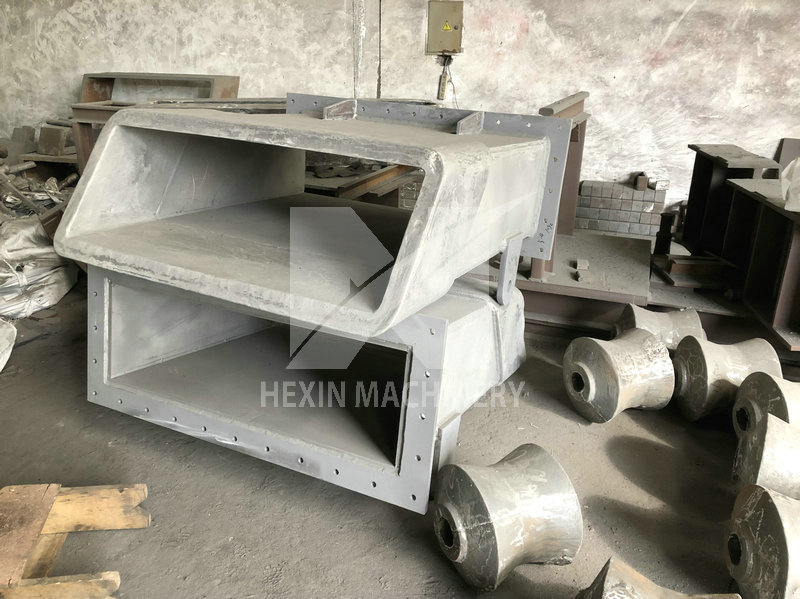
As a very effective steel anti-corrosion technology, hot-dip plating is used to coat a layer of metal or its compound on the surface of steel. Hot-dip galvanizing of steel began in the 1930s and has a history of more than 200 years. During this period, a variety of hot-dip galvanizing production processes were developed. With the continuous deepening and development of technology research, hot-dip galvanizing of steel has also become an important industry and has been widely developed. As a mechanized and highly automated hot-dip galvanizing technology, continuous hot-dip galvanizing is efficient and economical in the production of plates, wires and strips. Therefore, it is studied by the majority of scientific researchers. Continuous galvanized steel sheet can be divided into pure galvanized steel sheet-GI steel sheet and post-galvanized steel sheet-GA steel sheet. GA steel sheets are widely used in industrial production and automobile industry due to their good surface quality and excellent corrosion resistance. At present, my country has built a number of continuous hot-dip galvanizing production lines, providing a large number of high-quality galvanized steel sheets for automobiles at home and abroad.
The evaporation of liquid zinc in the furnace nose, the zinc vapor rises above the furnace nose, and condenses into liquid or solid zinc or zinc oxide when condensed, and continuously aggregates to form droplet-shaped zinc or zinc oxide, which drips on On the strip or zinc bath surface, the dross composed of iron/zinc/aluminum and the dross accumulated on the zinc bath surface adhere to the strip or zinc pot rollers and are eventually drawn into the galvanized layer.
In view of the above-mentioned deficiencies of the prior art, the technical problem to be solved by Qingdao Hexin Machinery Co., Ltd. is to provide a zinc boiler nose that can reduce various surface defects formed by zinc ash and zinc slag and increase the output.
To solve the above technical problems, the following technical solutions are provided:
A zinc boiler nose, including a PSE system, a cleaning port, a first window flange, a zinc pump bracket, a zinc tank, a front pipe, a rear pipe, a lining, a nut, a rod screw and a scrubber; the PSE system is provided in the furnace On the front right side of the nose body, a cleaning port is arranged on the upper right of the furnace nose body, and a first window flange and a second window flange are arranged on the upper left; After the part is set up the pipeline.
In this scheme, the special furnace nose system of the zinc pot includes specially designed furnace nose end, zinc liquid pump system, high-precision double liquid level detection, advanced automatic zinc adding device and the design of the guaranteed surface ash collecting tray. The special overflow design can realize the special inclination angle, the flow matching can be realized through the special zinc liquid pump system, and the precise liquid level control and liquid level control range can be realized through the high-precision double liquid level detection. The zinc-adding device ensures the high-precision control of the liquid level. In general, the special furnace nose system of the zinc pot has the following beneficial effects: a. Quality improvement - significantly reducing various surface defects formed by zinc ash and zinc slag, the outer plate The yield is significantly improved and the surface quality is better; b. No need to manually clean the zinc liquid in the furnace nose - there is no more slowdown and production reduction; c. More flexible production plan, as long as the composition of the zinc liquid is accurate, zinc The pot roll is in good condition, and the outer plate can be produced at any time; d. Increase in production capacity—the production speed of outer plate is greatly improved; in this embodiment, the "special furnace nose for zinc pot" can be used to build the furnace nose around the upper and lower surfaces and sides of the strip. Stable and continuous zinc liquid flow, so that the particles in this area and the oxidized suspended matter on the surface are effectively taken away from the surface of the strip steel, in addition, the "special furnace nose of the zinc pot" can bring longer outer plate production time , Shorter transition time from inner plate to outer plate and quick transfer to outer plate production after shutdown and restart.
The special inclination angle can be realized through the special overflow design at the end of the furnace nose, the flow matching can be realized through the special zinc liquid pump system, and the precise liquid level control and liquid level control range can be realized through the high-precision double liquid level detection. , through the advanced automatic zinc adding device to ensure the high-precision control of the liquid level, in general, the special furnace nose system of the zinc boiler has the following beneficial effects: a. Quality improvement - significantly reduce the various forms of zinc ash and zinc slag. Surface defects, the yield of the outer plate is significantly improved and the surface quality is better; b. No need to manually clean the zinc liquid in the furnace nose - no more slowdown and production reduction; c. More flexible production plan, as long as the zinc The liquid composition is accurate, the zinc pot rolls are in good condition, and the outer plate can be produced at any time; d. Increase in production capacity—the production speed of the outer plate is greatly improved; The upper and lower surfaces and sides establish a stable and continuous flow of zinc liquid, so as to effectively take the particles in this area and the oxidized suspended matter on the surface away from the surface of the strip steel. The production time of the outer panel is shorter, the transition time from the inner panel to the outer panel is shorter, and the production of the outer panel is quickly transferred after the shutdown and restart.