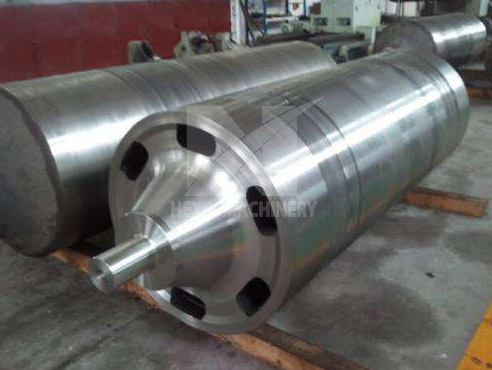
Cost-effective comparison of different surfacing technologies for sink rolls
For many sink rolls surfacing, the main thing is that they have different performance requirements. Generally speaking, for most of the surfacing welding of sink rolls, if we use a single material, it will not meet our requirements, and for its inner and outer layers, it can also be made of two materials separately.
If the sink rolls surfacing itself uses composite technology, it can use mechanical combination, as well as composite casting and other cladding technologies. But for its roll surface repair, it mainly adopts surfacing technology. For sink rolls bearing wear, if it is a relatively shallow situation, many companies use pitting or copper pads to cope with it.
Therefore, when we are surfacing the sink rolls, it is difficult for us to meet the wear size of 0.5mm, or the brush plating technology for bearing positions that exceeds this range. And if hot repair welding is used, its influence on the damage of our metal is relatively large. On the other hand, if the repair welding temperature and the repair welding times are not well mastered, the shaft will be deformed, and there may be a direct fracture and a great hidden danger.
The sink rolls are customized for surfacing welding. If it is a non-standard inner ring, the wear size of each sink roll is not uniform. As for the processing size of its customized non-standard inner ring, and its cost, our Rolling companies are very unbearable.
For the surfacing of sink rolls, no matter what kind of process and material it is, we have to distinguish the cost-effectiveness of surfacing of sink rolls according to a specific situation. Furthermore, for its practical application, it is also necessary to pay attention, we can avoid the possibility of its wear and tear, and the use time of equipment components can also be extended.